Top 10 der wichtigsten Schritte zu Ihrer Industrie 4.0 Strategie
Digitalisierung / Industrie 4.0Ein Praxis-Leitfaden für die Digitalisierung
Digitalisierung ist eine der größten Herausforderungen in Unternehmen. So gaben in einer Umfrage des Digitalverbands Bitkom anlässlich der CeBIT 2016 fast zwei Drittel (64 Prozent) der befragten Unternehmen an, dass sich infolge der Digitalisierung ihr Geschäftsmodell verändert. Im Vorjahr waren es noch 55 Prozent. Gleichzeitig sehen sich die Unternehmen aber kaum vorbereitet: Mehr als 60 Prozent der Unternehmen sehen sich als digitale Nachzügler.
Big Data, cyber-physische Systeme, Cloud und Internet of Things sind Schlagwörter, die häufig fallen. Aber was verbirgt sich dahinter? Und was bedeuten diese konkret für Unternehmen? Wir haben die 10 wichtigsten Schritte auf dem Weg zu Ihrer Industrie 4.0 Strategie zusammengefasst:
1. Maschinen vernetzen
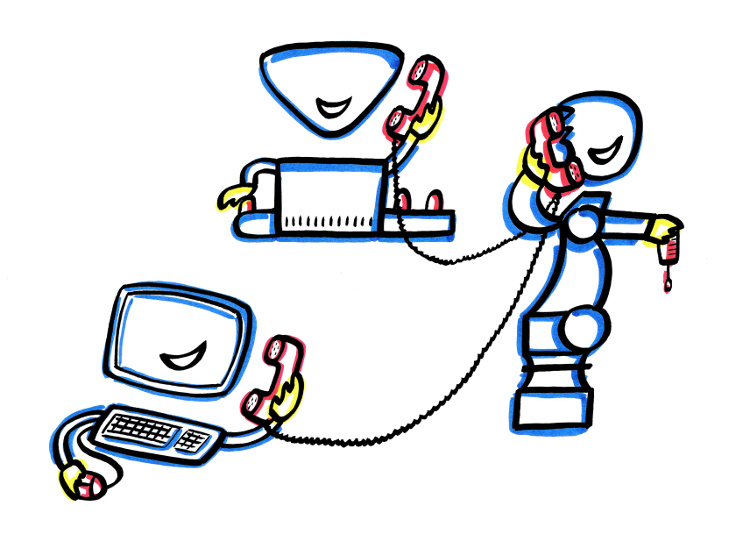
Cyber-Physische Systeme sind Voraussetzung von Industrie 4.0. Der Begriff meint die Kombination von mechanischen Komponenten – Werkteilen – mit Informationstechnik. Ziel sind intelligente Werkstücke, die virtuell erfasst werden können, um Daten zu sammeln und auszuwerten. Denn durch die Analyse von Daten können Unternehmen ihre Effizienz steigern – ein Wettbewerbsvorteil. Zu diesen Komponenten gehören etwa RFID-Chips, die in Bauteile eingelassen werden, um deren Weg durch die Fertigung und Logistik genau verfolgen zu können. Aber auch Sensoren und Aktoren in Maschinen gehören dazu. Wie Unternehmen solche Systeme nutzen können, um ihre Produktion zu optimieren, zeigt das BIBA – Bremer Institut für Produktion und Logistik in Bremen mit dem viel beachteten Demoprojekt CyProS.
2. Sicherheit schaffen

IT- und Datensicherheit ist eine der größten Hürden in der digitalen Transformation. Die Gefahren sind groß, denn unzureichend gesicherte Automatisierungstechnik kann zu großen Schäden führen, wie Stefan Menge vom Freie Institut für IT-Sicherheit e.V. verrät. Nur eine umfassend angelegte und im Voraus geplante IT-Sicherheitsstrategie schützt das Unternehmen im ausreichenden Maß. Wie diese Sicherheit geschaffen werden kann, verrät der Leitfaden IT-Sicherheit.
3. Kommunikation vereinfachen
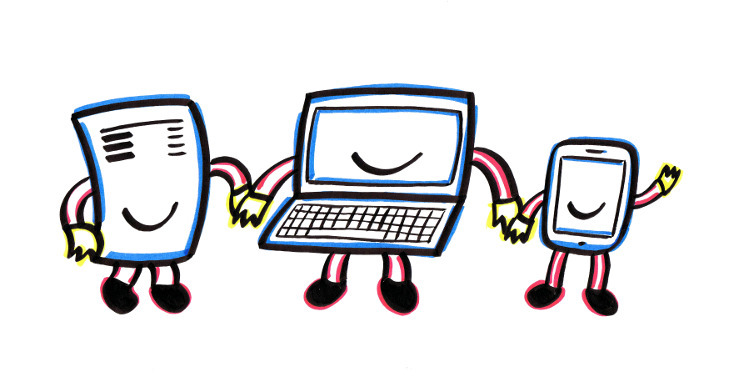
Damit autonome Systeme entstehen können, müssen sie miteinander kommunizieren können. Eine der größten Herausforderungen von Industrie 4.0 ist es deshalb, einheitliche Standards zu schaffen mit denen Systeme von verschiedenen Herstellern und aus verschiedenen Produkt-Generationen miteinander reden können. Denn Insellösungen – geschlossene Systeme von einem einzelnen Hersteller – sind nicht anpassungsfähig genug, um den wechselnden Anforderungen durch die Digitalisierung zu genügen. Wie Forschungsinstitute wie das Bremer Technologiezentrum Informatik (TZI) an neuen Standards arbeiten, erklärt Armin Dekorsy, Leiter des Arbeitsbereichs Nachrichtentechnik am TZI. Entscheiden sich Unternehmen für eine neue Digitalisierungsstrategie sollten sie daher darauf achten, dass die Soft- und Hardware möglichst schnittstellenoffen ist.
4. Individueller und schneller produzieren
Alle Komponenten unterhalten sich miteinander. So entstehen autonome Systeme. Etwa im Straßenverkehr auf dem Weg zum autonomen Fahren. Oder in der Fabrik, wo Maschinen selbstständig Nachschub ordern oder ihre Auslastung organisieren. Das ist wichtig, denn in der Fabrik der Zukunft ist die Losgröße 1 das Ziel: Verbraucher können sich Produkte, Unikate, nach ihren Vorstellungen zusammenstellen. Das ist heute bereits in der Automobil-Industrie Standard, wo Kunden aus tausenden von Extra-Optionen wählen. Um diese Vielfalt zu bewältigen, müssen sich die Maschinen in einer Fabrik selbst organisieren. Welchen Weg ein Bauteil durch die Fabrik nimmt, entscheidet nicht ein zentraler Produktionsplan, sondern das intelligente Bauteil selbst. So können Aufträge sehr viel schneller abgearbeitet, aber auch noch spontan bis zur letzten Sekunde geändert werden. Was maximale Flexibilität für die Fabrik der Zukunft bedeutet, erläutern die Fabrikexperten von der GPS Planfabrik in diesem Interview.
5. Arbeit erleichtern
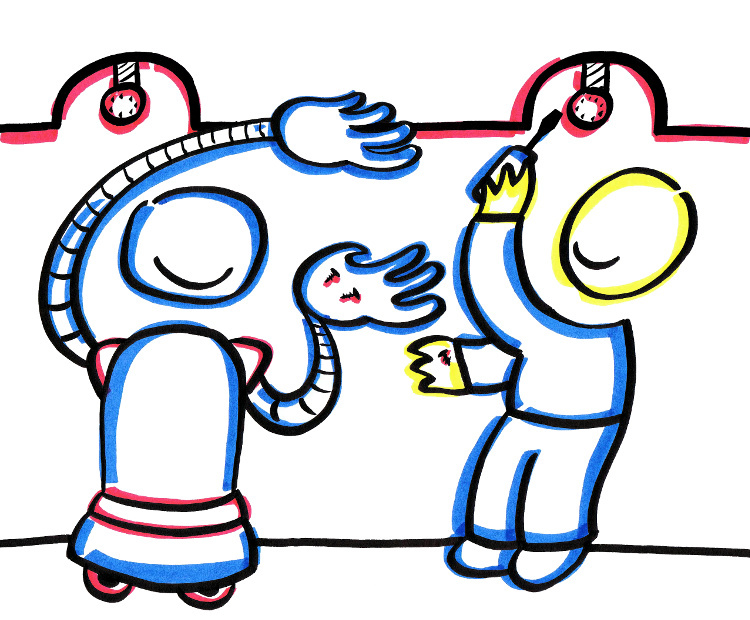
Industrie 4.0 bietet die Chance, Arbeitsprozesse entscheidend zu vereinfachen. Mensch-Roboter-Kooperationen werden überall dort künftig Standard, wo automatisierte Fertigung allein nicht möglich ist. Etwa im Flugzeugbau, dessen Produktion eher einer Manufaktur gleicht als einer Fabrik – wie der Airbus-Standortleiter Bremen, André Walter, im Interview erklärt. Während in der Vergangenheit der Mensch die Maschine bediente, kehrt sich nun das Verhältnis um: Die Maschinen bedient den Menschen. Roboter helfen, Bauteile an schwer erreichbaren Stellen zu fixieren, etwa über Kopf. Das verbessert die Ergonomie, senkt die Gesundheitsgefahren und erhöht die Arbeitssicherheit. Einer, der daran forscht, ist Dr. Sebastian Bartsch vom Deutschen Forschungszentrums für Künstliche Intelligenz.
6. Daten auswerten
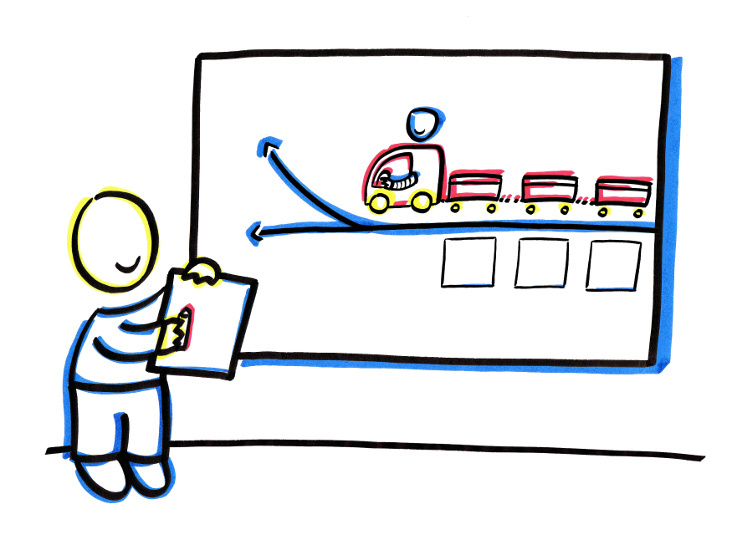
Das Internet der Dinge produziert eine große Menge an Daten – die ausgewertet werden müssen. Hier helfen virtuelle Agenten. Sie sind nichts anderes als eine virtuelle Darstellung aller Maschinen, Bauteile und Akteure – ob Menschen oder Roboter. Reale Daten werden in diese Simulation eingespeist. Der Clou: virtuelle Agenten sind intelligente Programme – die künstliche Intelligenz optimiert die echte Fertigung. Hier vermischen sich Realität und Simulation – beide Prozesse bedingen einander und verbessern sich so ständig.
Das gilt nicht nur für die eigene Fertigung: Prozesse müssen ganzheitlich betrachtet werden. Dazu gehört es zum Beispiel, Schnittstellen zu Lieferanten, aber auch Kunden aufzubauen. So können Unternehmen Logistikprozesse vereinfachen oder die Nachbestellung von Auftragsteilen automatisieren. Schlüssel zur digitalisierten Plattformen ist die Cloud: Auf sicheren Verbindungen können so Daten in Echtzeit miteinander ausgetauscht werden.
7. Offen sein für Veränderungen
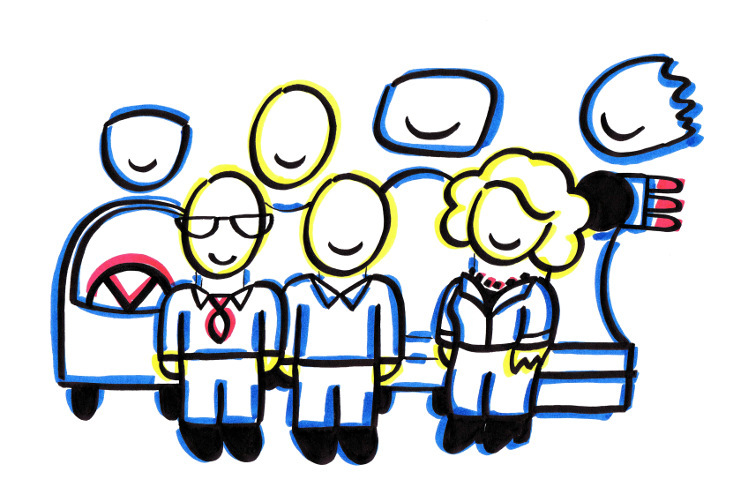
Mit der Digitalisierung ändern sich auch die Unternehmensprozesse – neue Geschäftsmodelle entstehen, neue Produkte und Vertriebswege entwickeln sich. Das wirkt sich auf die gesamte Unternehmensstruktur aus. Flachere Hierarchien, dezentrale Strukturen und interdisziplinäre Teams bilden sich häufig aus, um die agilen Entwicklungen der digitalen Transformation zu bewältigen: Wer dynamisch sein will, muss auch dynamische Strukturen schaffen. Das Management und die Unternehmensführung müssen diese Veränderungen zulassen und unterstützen. „Es ist wichtig, eine Digitalkompetenz aufzubauen, für den Mitarbeiter, für die Führungskräfte und die Gesamtorganisation“, sagt etwa Sven Voelpel von der Jacobs University.
8. Mitarbeiter qualifizieren
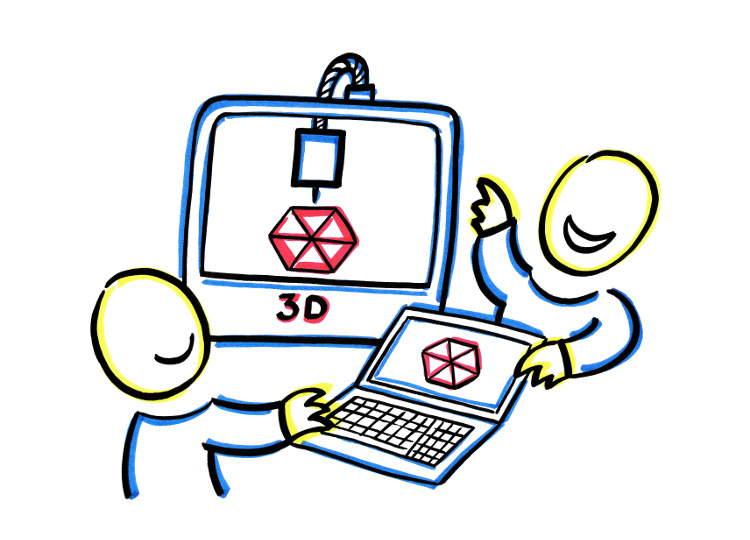
Auch in der Zukunft braucht die Fabrik Arbeiter. Qualifizierte Arbeiter – mit anderen Qualifikationen als heute. Wissensintensive Arbeit nimmt zu, während monotone, gleichförmige Arbeiten abnehmen, egal ob an der Drehbank, in der Buchhaltung oder im Marketing. Schon heute können Computer Sportnews und Börsenberichte schreiben. Unternehmen müssen ihre Belegschaft deshalb regelmäßig weiterbilden - Lebenslanges Lernen. Dazu gehört etwa die Ausbildung am 3D-Drucker.
9. Geld verdienen
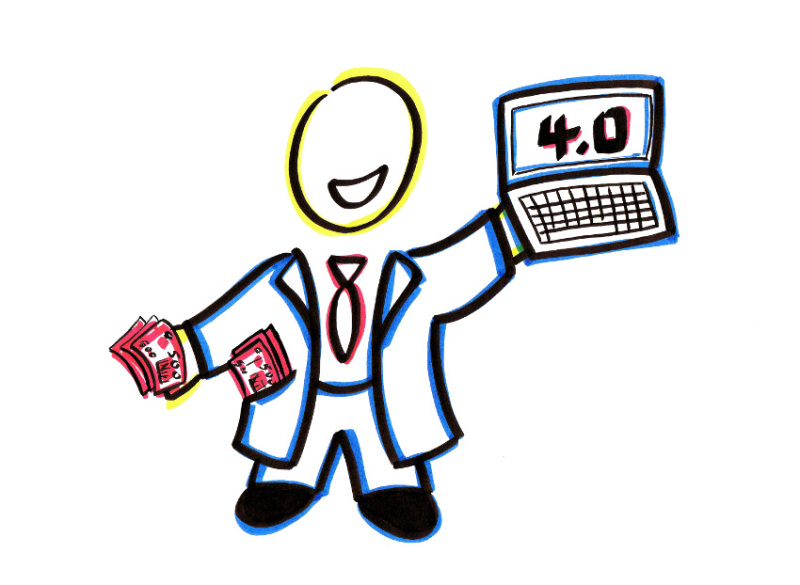
Durch die Digitalisierung wird es möglich sein, auf ganz neue Weisen Geld zu verdienen. Denn das bedeutet: Wettbewerbsfähigkeit erhalten. Auf der einen Seite können Preise gesenkt werden, indem Effizienzgewinne genutzt werden. Viel wichtiger sind jedoch neue Geschäftsmodelle, die sich durch Digitalisierung ergeben: Neue Services und Angebote, die vorher nicht möglich waren. Bestes Beispiel ist Uber aus den USA, das größte Taxiunternehmen der Welt – ohne ein einziges Taxi zu besitzen. Es nutzt die digitale Welt – mobile Apps und lokalisierte Daten – um Fahrer und Fahrgäste zusammenzubringen. Oder General Motors, das nach einer erfolgreichen Insolvenz im Jahr 2009 heute wieder eine halbe Milliarde Euro in den Uber-Konkurrenten Lyft investierte und sich heute als Mobilitätsanbieter und nicht nur als Autobauer positioniert.
10. Einfach loslegen
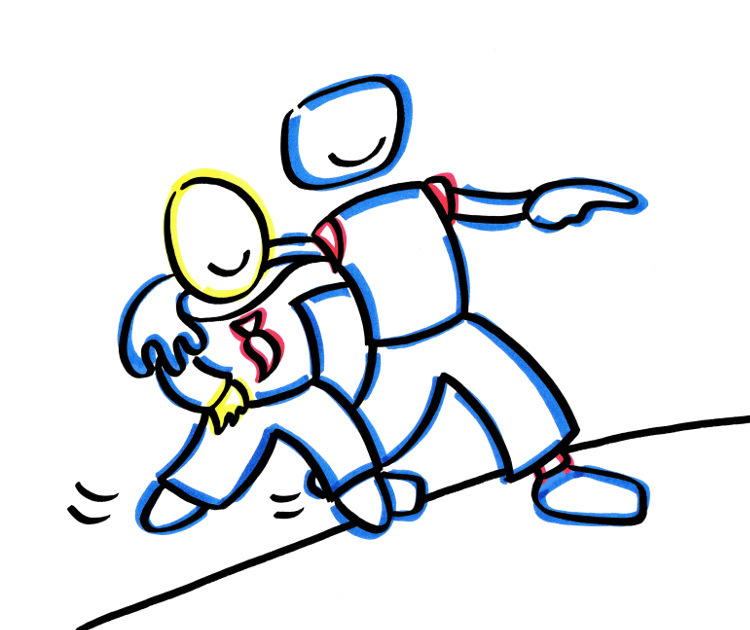
Zentraler Anspruch von Industrie 4.0 ist es, die Effizienz zu erhöhen, schneller und qualitativ hochwertiger zu produzieren. Die Digitalisierung bietet die Chance, Kommunikationswege zu vereinfachen und zu vereinheitlichen. Und das auch im kleinen Maßstab: Die Frage, die sich Unternehmen dazu stellen müssen sind: Wo gibt es in meinem Unternehmen Medienbrüche? Wo muss ich Daten von Hand von einem Medium ins andere übertragen? Genau hier sind erste Ansatzpunkte zur Digitalisierung. Am Ende ist es ganz einfach: Digitalisierung beginnt im Kleinen. Ein Testprojekt oder eine erste Idee lassen sich so schnell identifizieren. Alles weitere kommt danach – wie es weitergeht, zeigt der Leitfaden Industrie 4.0.
Grafiken von Janine Lancker, fliplance
Welche Services die WFB Wirtschaftsförderung Bremen GmbH bei der Digitalisierung ihrers Unternehmens bietet, finden Sie auf der Übersichtsseite Digitalisierung.
Erfolgsgeschichten
Von der Elbe an die Weser: Wie LITE Games in Bremen neue Spiele-Horizonte erobert
Das Unternehmen LITE Games bringt Klassiker wie Rommé als moderne Mobile Games zurück – mit frischem Design und smarten Features. Geschäftsführer Michael Becker setzt dabei auf zukunftsweisende Technologien und die kreative Kraft Bremens. Bei der Ansiedlung in der Bremer Überseestadt unterstützte die WFB.
Mehr erfahrenKI in der praktischen Anwendung – ein Blick in die Bremer Branchen
Künstliche Intelligenz (KI) dringt ein in unsere Autos, Zahnbürsten, Produktionsanlagen und Büros. Wo ist sie schon Unternehmensalltag? Beispiele für KI in der Anwendung.
Mehr erfahrenSchlaues Tool hilft Rathäusern und Ratsuchenden - Bremerhavener Start-up treibt Digitalisierung in Behörden mit KI voran
Die Arbeit von Behörden wird immer komplexer; parallel wächst der Informationsbedarf in der Bevölkerung. Zwei Studierende der Hochschule Bremerhaven treten diesem Dilemma mithilfe von KI entgegen.
zur BiS Bremerhaven