When precisely isn’t quite precise enough
Success storiesEickworth Modellbau builds testing equipment and tools for the automotive and aerospace industries.
When Peter Eickworth and André Kuhn, the two executive directors, stroll through the Eickworth Modellbau factory they are surrounded on all sides by humming, buzzing, howling and rattling. CNC machines the size of garages mill components out of huge, heavy aluminium blocks in a relentlessly meticulous process. The employees produce, assemble and test until everything fits precisely, down to a hundredth of a millimetre.
“The diameter of a hair is seven hundredths of a millimetre, but that level of accuracy would be totally inadequate for our measuring equipment. A hair’s breadth is nowhere near accurate enough for us,” Peter Eickworth says proudly. The executive director of Eickworth Modellbau represents the third generation of his family in charge of the company. Precision is his blood.
Enabling testers to test
Eickworth is an important partner for the automotive and aerospace construction industries. The long-established Bremen company produces testing and measuring equipment, as well as gauges for quality assurance. These are forms or fixtures into which work pieces, e.g. those used by Mercedes on their production lines, can be inserted before assembly to test their size and interfaces for accuracy.
QA departments of manufacturing companies and suppliers use them continuously to check that the size of components remains constant. Their aim is to detect errors in the production process before they are replicated thousands of times. To ensure that these measuring devices always produce correct results, Eickworth uses far greater precision in their production than is required for the components they will be used to test later on, such as mudguards, for example. They set themselves very high standards, and have been meeting them since 1920.
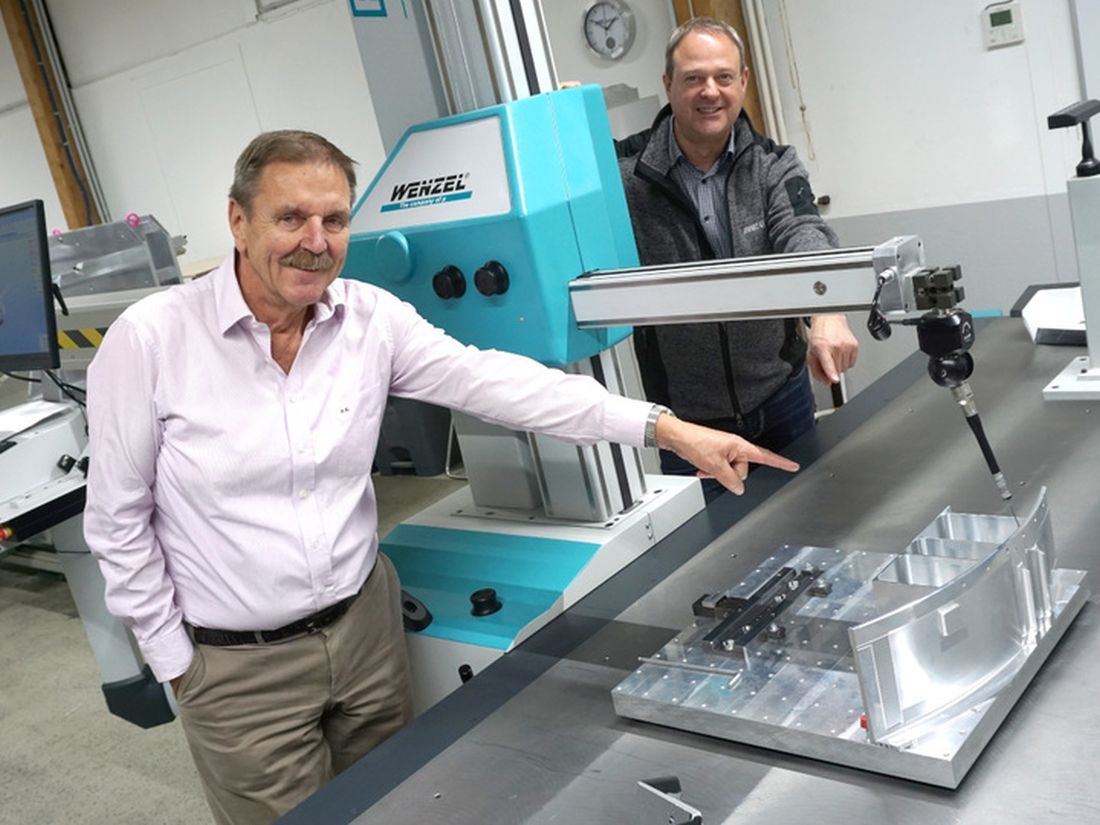
A steady stream of one-off pieces
In addition to testing equipment, the company produces tools for forming and injection processes, and refines and produces components as well as fixtures for production tools. One example is a bracket into which a milling robot at Mercedes can insert components to work on them.
Besides major car manufacturers like Mercedes and VW, customers also include Airbus and the satellite manufacturer OHB. Components linked to products from Eickworth Modellbau are included in almost every aircraft model series, from the A380 and the A400 military transport plane all the way to the Eurofighter. The Bremen company cannot afford any mistakes. “Almost every component is unique. Our testing equipment is normally only required once in every factory. That makes our work very challenging,” explains André Kuhn, the company’s other executive director.
The company’s skills are particularly impressive when you consider the dimensions they are working with. Some forms are several metres long and weigh more than a tonne once their transport frames are included. These are used for high-lift devices in aircraft construction, e.g. for the landing flaps of Airbus planes.
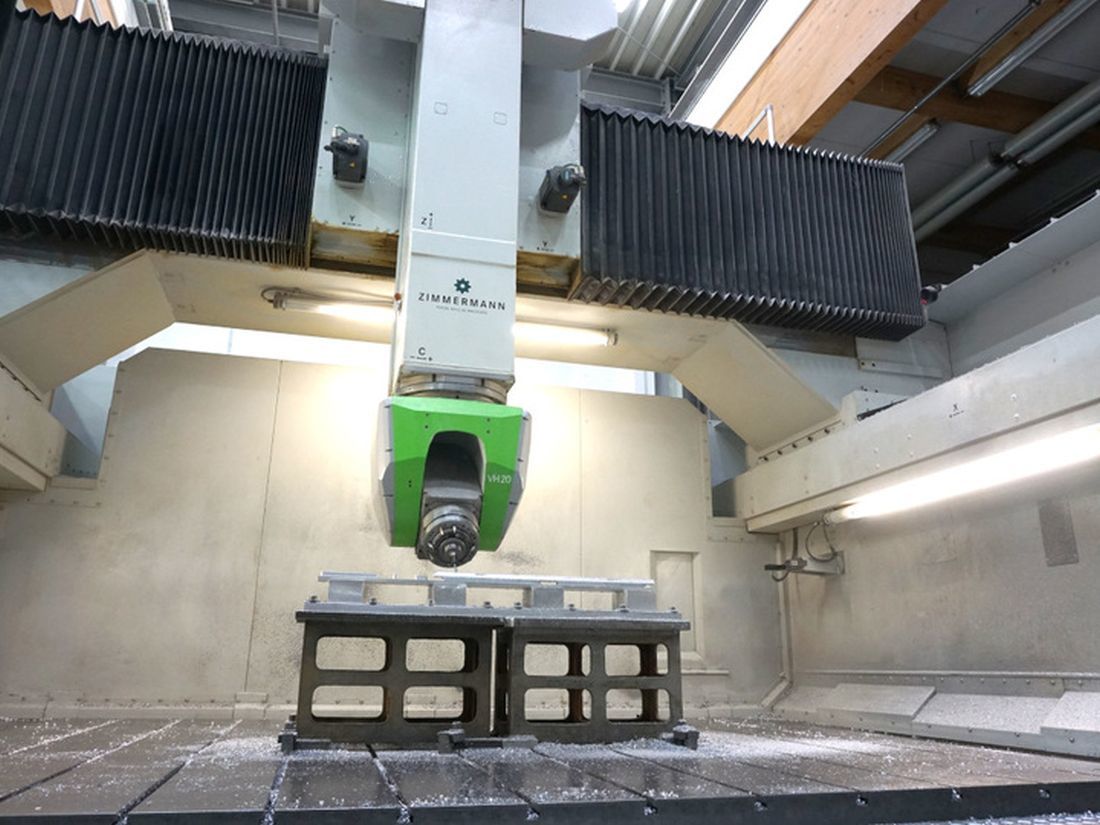
Well-versed in working with many different materials
“When I get on a plane, I am proud to know that it includes parts for which we have produced test gauges and tools,” says Kuhn. Before long, Eickworth components will even be heading to the moon. The 49-year-old executive director, who trained as a toolmaker, is also proud of some of their more recent acquisitions. There’s the conversion and extension of their office building, which now boast a spacious meeting room and a cutting-edge design and planning department. And then there is a CNC-controlled 3D measuring machine that can be extended to up to four metres.
The forms and fixtures are made from a range of different materials: aluminium, steel, plastic, composite materials and even wood. “Wood still plays an important role in aircraft construction. We make tools used for forming aluminium and titanium parts from compreg. This compressed and processed ‘wood’ has excellent flow characteristics and isn’t too hard,” explains Peter Eickworth, who took over the business from his father in 1980 and has driven the transition towards digital, computer-aided production over the past 38 years.
At the heart of the digital revolution
With all that precision it is hardly surprising that nine of the 50 employees are entirely computer-based, working as CAD engineers and CAM programmers. They design the testing equipment, and then the CNC milling machines get to work. “We normally receive a 3D item from our customer and then we design the corresponding form or fixture, while adhering to any relevant specifications. So we need to ask ourselves: ‘How can I test this item quickly and accurately?’ That is always a challenge,” says Eickworth.
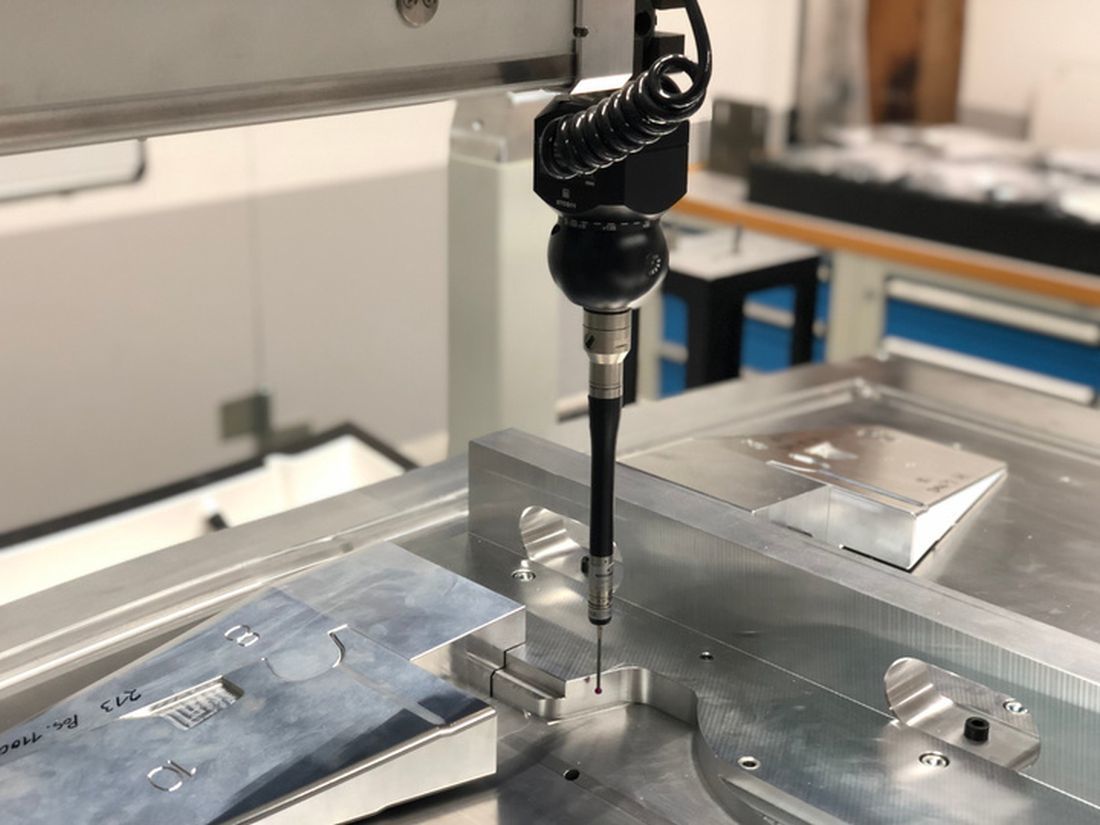
For the last few months, the company has also been experimenting with 3D printing. At the moment they are printing in plastic – mock-ups and smaller models, for example – but in future perhaps also in metal. “We follow where our customers lead, so we are constantly evolving,” says Kuhn.
Into the future with BAB
That evolution has solid foundations. Since 2012, Eickworth Modellbau has been working with BAB – the development bank for Bremen and Bremerhaven. The measurement experts were able to finance the acquisition of a CNC measuring machine and a ten-metre-long CNC portal milling machine – probably one of the largest of its kind in Bremen – thanks to a grant and a loan from the LIP regional investment programme. The latest extension to the office wing at their premises in Bremen-Arsten business park in 2016 were also part-financed through this programme. Peter Eickworth sums it up: “It’s been a very pleasant, smooth cooperation. Thanks to the financing we received, we are perfectly positioned to face the future.”
The only thing that worries the two executive directors is the shortage of skilled workers, so as a training organisation they are doing everything they can to produce the next generation of model makers and design engineers for precision engineering made in Bremen. No matter what technologies they will be using, one thing is certain: precisely will still not be precise enough.
If you have questions about the LIP regional investment programme, please contact Ina Meier-Buick, +49 (0)421 9600 227, Ina.Meier-Buick@bab-bremen.de.
Success Stories
8 Bremen Companies involved in Mass Spectrometry
If you want to get down to the smallest building blocks of our world, you need mass spectrometers. And there are few places in the world where there is such a high concentration of specialists and manufacturing companies and suppliers in this sector as in Bremen.
Learn moreNine products from Bremen that nobody has heard of, but everyone uses
Products made in Bremen can be found in many everyday objects, and most of us are likely to come into contact with one or more on a daily basis. Read on to find out what they are.
Learn moreClockwise opens its first German location in Bremen: Flexible coworking with a regional flair
The British company Clockwise has opened its first German location in Bremen. With locations in London, Belgium, The Netherlands, and now on Martinistraße in the city center, the company follows a clear vision: to create workspaces that are flexible, welcoming, and tailored to the needs of modern professionals.
Learn more