A visit to ArcelorMittal’s Digital Lab in Bremen
Digitization
3,100 employees, around 3.5 million tonnes of steel, and a site that covers seven square kilometres – this steel plant in the north of Bremen boasts some impressive numbers, not least in terms of its size. With so much ground to cover, bringing this plant into the digital age is no mean feat.
Still, a year and a half ago, the company set up a team to do exactly that. Its task is to introduce new digital technologies throughout the organisation. Last year, the team even acquired its own offices, the Digital Lab.
Digilabs – making the most of local expertise
ArcelorMittal, an international steel producer, has digitalisation teams at many of its sites, the idea being that each one contributes something to the digital transformation of the Group as a whole. Instead of a centralised innovations management imposing new technologies from above, in this approach each site can determine for itself which technology is going to take it forward. Every plant has a digital officer, whose job includes sharing any findings with the other plants, thereby facilitating the transfer of expertise. In Bremen, they have also adopted the Digital Lab approach, in other words, digitalisation from the bottom up. One major advantage of this is that the solutions are actually applied, since they are rooted in practical experience.
Parts tracking with RFID
Dr Jens Ehm, head of the Digital Lab in Bremen, offers an example. His team has been testing the use of RFID tags in the hot rolling mill, a one-kilometre building where steel ingots are rolled into strips. The tiny transmitters allow the contactless identification of objects, similar to a barcode on a carton of milk. At the plant, they are attached to the rollers that transform the steel, which require regular maintenance. “At the moment, the rollers are labelled and documented manually. The RFID transmitters allow us to automate the wireless tracking of their journey,” says Ehm. That saves time and effort, and avoids potential mix-ups.
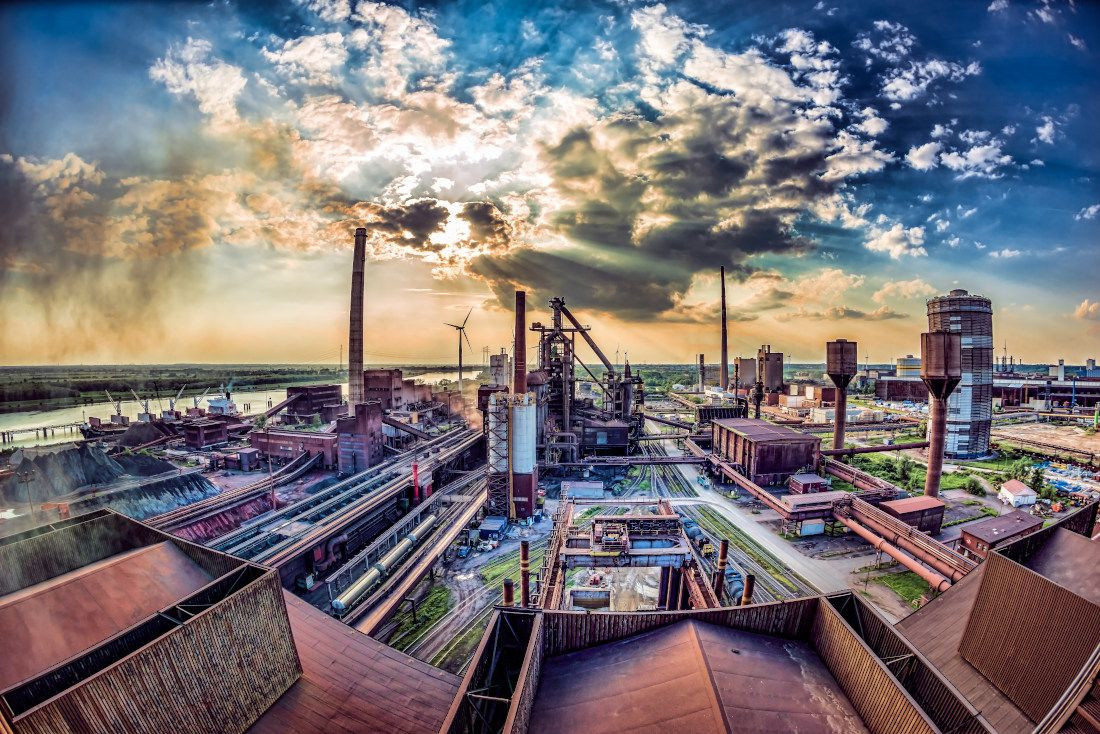
Creating a designated space for experimentation
How does that sort of project come into being? The Digital Lab plays a key role. The 85 square metre office contains a meeting area, a workshop space, several workstations and the latest technology. Staff from different departments regularly get together here to discuss digital topics. It’s a place where they can upgrade their skills, experiment and get creative. The most promising ideas will be developed into a proof of concept to determine their feasibility. The digitalisation team either develops ideas in collaboration with their colleagues or draws on the help of external partners to create an initial prototype. If that can be made to work, and the concept has demonstrable production potential, then the concept phase ends and the project is handed over to the relevant department which continues to develop it.
The Digital Lab is like an incubator where new ideas are able to blossom, away from the pressures of day-to-day production. There is a dedicated budget for digital projects – vital for providing scope for experimentation, as not every innovation project is going to be successful.
Data network with a vast range of applications
There are currently about 30 proofs of concept being worked on in Bremen, at varying stages of development. One of Jens Ehm’s favourite projects is related to LPWAN technology, which stands for ‘low power wide area network’. It’s a wireless network with a very low bandwidth, but a very large operating range and extremely low energy consumption. “It is perfect for sensors to be distributed all around our vast site which can then provide regular status updates.” That could be the location of a container, the reading of an electricity meter or the water level in a shaft. A single antenna is enough to cover the entire site and thousands of sensors. The technology provides the company with a better overview of its site, and improves its reaction speed.

Artificial intelligence (AI) in steel production
At ArcelorMittal Bremen they are also following the debate around AI with a great deal of interest. “We take a fairly pragmatic approach, and try to see where we might actually be able to apply AI technology. Artificial intelligence is a very trendy topic – we’d rather skip the hype and go straight to the real application,” says Ehm. His team are already testing some initial image recognition tools. One thing is clear: “AI will support our employees in a wide variety of ways, for example in terms of health and safety at work. We are currently developing assistance systems, for example.”
The team regularly attends events organised by the Bremen.AI network. “Bremen is a strong AI location, and we feel it’s important to keep track of the latest developments and where their potential lies. That is why we share information with other digital labs in Bremen,” explains Ehm. His team have had some initial contact with the digilab of another major Bremen employer, and are hoping for further collaborations.
A model for digitalisation
The steelmaker’s approach is a great example of how to implement the digital transformation of industry (known in Germany as Industry 4.0). New ideas and solutions are suggested by the users, who are best placed to know the challenges of their respective workplaces. But the initial development takes place in a protected space, separate from day-to-day working life, which provides a chance to experiment.
Instead of obeying centralised edicts, the individual departments can work independently on their own challenges – which improves acceptance. Solutions are only rolled out to different production sites once they have been fully developed. All of these factors together make bottom-up digitalisation possible. This strategy is equally suitable for small and medium-sized enterprises that have only limited resources – on a smaller scale, of course.
Success Stories
“After all, we're here because someone else made room for us, and it's our duty to do the same for others”
Theoretical physicist, industrial mathematician, manager – as a member of the start-up company TOPAS, Dr. Shruti Patel creates change in Bremen. However, being a role model has not always been easy for her.
Learn more12 Examples of AI in Medicine and the Health Sector
Detecting cancer earlier or avoiding accidents at work - AI will make our lives easier and easier in the healthcare sector. In Bremen, a strong AI landscape is developing in the healthcare sector, as these 12 examples show.
Learn moreThese Bremen companies are developing autonomous systems
Self-driving cars, drones, robots - in Bremen, autonomous systems are a focus of numerous focus of numerous companies. A look at the diverse corporate landscape and where the committed players can be found.
Learn more